Rejuvenating Europe's electrical grids with composites
Roughly one third of electrical grid infrastructure in Europe is over 40 years old, with this share expected to surpass 50 per cent by 2030. This means it was not built to handle the increasing electricity consumption of modern Europe and renovating infrastructure is a high priority. Here Heini Kloster, our Product Business Owner for electrical solutions, offers an insight into how composites can support the rejuvenation of Europe’s electrical network infrastructure.
Electrical network infrastructure throughout Europe has seen better days, with significant portions of networks several decades old and struggling to cope with increasing demand. This problem only continues to worsen due to global trends such as electrification and decentralized energy production. With tens of thousands of kilometers of overhead power lines throughout Europe, the scale of the problem is huge, and the electrical industry must turn to new technologies to prepare the networks for the future.
To make matters worse, environmental factors like high-speed winds and extreme temperatures are becoming increasingly common because of the impacts of climate change and the grid infrastructure is not immune to the effects of these. New solutions for the infrastructure allow the grid to increase capacity, limit the risk of structural damage and ease maintenance and rebuild.
Composite solutions for electrical grid infrastructure
Fiber glass composites hold significant potential for many electrical applications due to the material’s high electrical insulation. For example, high-voltage power transmission lines that carry up to 400 kV necessitate high amounts of insulation to protect people and sensitive electrical equipment around power transmission lines of varying voltage levels, including transformers and substations. Along with the supporting structures, fiber glass composites can be used for insulators, fuse cut-outs and electrical tools like hot sticks as well as for transformer applications.
However, for conductor core applications, carbon fiber is more suitable because of its superior mechanical properties. Carbon fiber has a high stiffness to weight ratio and low thermal expansion, meaning it can tolerate high temperatures, something that is advantageous in conductor materials. Using carbon fiber allows the cross-sectional area of the conductor to be increased, creating more distribution capacity to handle the increased electrical demand.
Different kinds of tubes, crossarms, insulator rods and conductor cores can all be produced using pultrusion, which, as a continuous manufacturing process, is well suited to consistent, high-volume production of composite profiles. In the pultrusion process, strands of glass or carbon fibers, mats or technical fabrics are pulled together, saturated with resin, and then pulled into guides that feed into a heated die to cure the composite, which is then cut to the desired length.
Other components, like fuse cutouts or utility poles, can be manufactured using pull-winding, which is a continuous process, like pultrusion, and boasts an output at least ten times greater than filament winding. Cross-directional control of mechanical properties makes pull-winding the ideal manufacturing process for composite tubes where wall-reinforcement is needed. The final product will be lightweight and less resources are wasted during the manufacturing process compared to the traditional filament winding. The production speed is also significantly higher, which helps to keep the production costs manageable.
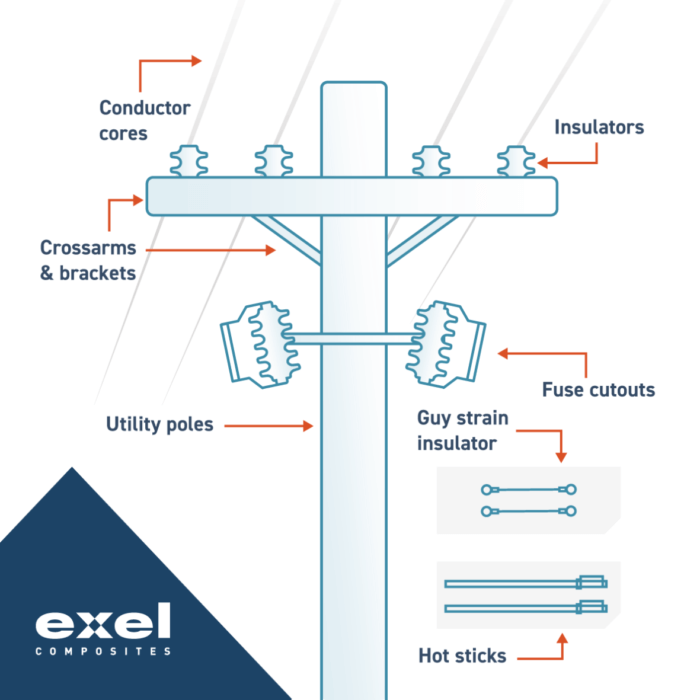