Reaping the benefits of pull-wound composite poles in utility infrastructure
There comes a point in the life of every business where it must scale its operations to continue growing. With telecommunications and utilities, this limit can be the difference between success and failure. When Telecommunications and utility pole specialist, EasyStreet Systems needed to scale manufacturing of its carbon fiber composite utility poles, it turned to pull-winding specialist Exel Composites.
EasyStreet Systems specializes in providing and installing small cell infrastructure solutions using advanced composite materials. The company’s towers, previously constructed from carbon fiber, serve as versatile platforms for a wide range of applications, including 4G/5G small cell deployments, IoT sites, and smart city initiatives. Composites are used in their products to deliver lightweight, durable, and aesthetically pleasing infrastructure solutions.
The company also offers customization for each installation, providing the flexibility to integrate a diverse array of technologies. From basic security cameras to smart lighting, all the way to sophisticated light detection and ranging (LIDAR) sensors, Wi-Fi access points, electric vehicle chargers, and power meters. This provides comprehensive solutions that address the evolving needs of modern infrastructure projects.
In the UK alone, the telecom market is estimated to grow by nine billion dollars in the next five years, and the Government is targeting total fiber coverage by 2033. As the demand for small cell infrastructure skyrockets, EasyStreet Systems faced limitations in its production capacity due to its reliance on carbon fiber. Despite the material’s initial advantages, its slow production process became a bottleneck, impeding EasyStreet Systems’ ability to scale and meet market demands. This predicament prompted a pivotal decision over material choice — one that led to a collaboration with specialist composite manufacturer Exel Composites.
“Carbon fiber filament winding was too slow for our production needs, and we wanted a single source that could produce all of our product, while maintaining quality control,” explained Kent Harrison, CTO of EasyStreet Systems. “We had to search for a supplier that could meet our demand, we needed a solution that could be produced quicker and cheaper but would perform equally well.”
Pull-wound composite poles
Exel, an industry leader specializing in continuous manufacturing of composites, emerged as a partner in addressing EasyStreet Systems’ production challenge. As a frontrunner in pultrusion and pull-winding composite manufacturing, Exel was uniquely positioned to provide tailored solutions that would not only meet but exceed the expectations of EasyStreet Systems.
“The brief from EasyStreet Systems to Exel Composites revolved around the need for a material solution that could match the strength and lightweight properties of carbon fiber while addressing the production constraints that were hindering business scalability,” explained Juha Pesonen, telecommunications segment owner at Exel Composites.” The challenge prompted us to innovate and develop a solution that not only met but surpassed the stringent requirements outlined in the brief.”
Exel proposed a solution leveraging the pull-winding manufacturing technique to produce glass fiber composite utility poles. In addition to the unidirectional alignment of fibers, the pull-winding process uses helical winding of reinforcements. This mix of fiber directions allows for advantages such as thinner walls and meeting specific strength or stiffness requirements. In EasyStreet’s case, pull-winding enabled poles that, while 25 per cent heavier than carbon fiber, were still lighter than traditional steel and wood poles and boasted superior strength and durability. For example, fiberglass composites exhibit a higher strength-to-weight ratio, with flexural strength reaching up to 1000 MPa compared to steel’s 370-520 MPa.
Furthermore, Exel’s pull-wound fiberglass poles offered tangible benefits in terms of installation efficiency. The weight of fiberglass poles makes them easy and quick to install, reducing installation time by up to 70 per centcompared to steel poles. The lightweight nature of fiberglass composites means that its installation requires minimal equipment and personnel for installation, translating into cost savings and accelerated project timelines.
Meeting tough quality standards
The Exel team encountered several challenges during the development and implementation of the utility poles, primarily related to regional standards and manufacturing optimization. For example, the wind speed, temperature, and climate in the northern US is completely different to that in the south, necessitating different infrastructure standards to manage the difference in conditions. Meeting these standards required rigorous testing and certification processes to adhere to industry regulations effectively in a single product, rather than producing different tubes with different properties dependent on the region.
Another of the technical challenges faced was addressing wind deflection and stability in the utility poles, crucial factors for their performance, especially in high wind-speed environments. Traditional filament winding techniques resulting in transverse fiber orientations, leading to pole deflection under high wind loads whereas pull-winding makes it possible to place and align fibers in axial directions due to the thin transverse layers leaving room for the axial fibers. This enhances the pole’s rigidity, reducing wind deflection.
Extensive simulations were conducted to assess the wind deflection characteristics of the poles under various conditions. These simulations, using Finite Element Analysis (FEA) tests, provided valuable insights into the structural behaviors of the poles and informed design refinements to augment performance.
By making the wall thinner and improving material usage through pull-winding, the Exel team achieved the same wind-deflection targets as the original carbon fiber tubes with less material used compared to traditional pultruded glass fiber poles, further reducing the overall weight to be closer to that of a similar carbon fiber tube. Additionally, as pull-winding is a continuous process, it allowed for the efficient production of large volumes enabling Exel to meet the demand of EasyStreet Systems while maintaining consistent quality.
Saving time, costs, and resources with composites
The collaboration has resulted in significant benefits for EasyStreet Systems’ utility infrastructure projects.
Exel Composites’ establishment of an ISO9001:2015 compliant manufacturing facility in the USA has bolstered EasyStreet Systems’ production capacity, resulting in shorter lead times, and improved operational efficiency.
EasyStreet has successfully implemented fiberglass composite utility poles, including an intersection in Peachtree Corners, GA, U.S. in collaboration with the Curiosity Lab at Peachtree Corners. As well as showing superior strength and resilience, the lightweight design of these poles has streamlined handling and installation processes, optimized resources, and reduced installation costs by 60 per cent, and installation time by up to 70 per cent compared to traditional steel poles.
Moreover, the use of composite poles eliminates the need for toxic preservatives normally associated with wooden poles, as well as doubling the lifespan of these telecommunications poles to 70 years, compared to the assumed 30–40-year lifespan of wooden poles. This, along with the local manufacture and lightweight nature of the poles, contributes to an overall carbon footprint reduction, while the continuous manufacture of the poles enhances material usage and minimizes waste.
Glass fiber composites are also compliant, the material is accredited by the National Electric Safety Code (NESC 2012) as being as reliable as steel equivalents. The material has also been recognized for its grid resilience in extreme weather, its high dielectric strength and 80 per cent lighter than steel and two hundred per cent stronger than wood.
“As a result of this collaboration, we can produce poles much quicker than before, as well as save money due to the price difference between glass fiber and carbon fiber,” added Pete Chase, CEO at EasyStreet Systems. “We have already rolled this out in Georgia at the Curiosity Lab at Peachtree Corners, and based on that success, we are working to roll out the product commercially in the UK and US.
“The next steps are to branch out into different sized poles and poles for different uses; we have already received requests for poles with smaller diameters for a smaller footprint, or a greater strength than traditional poles.”
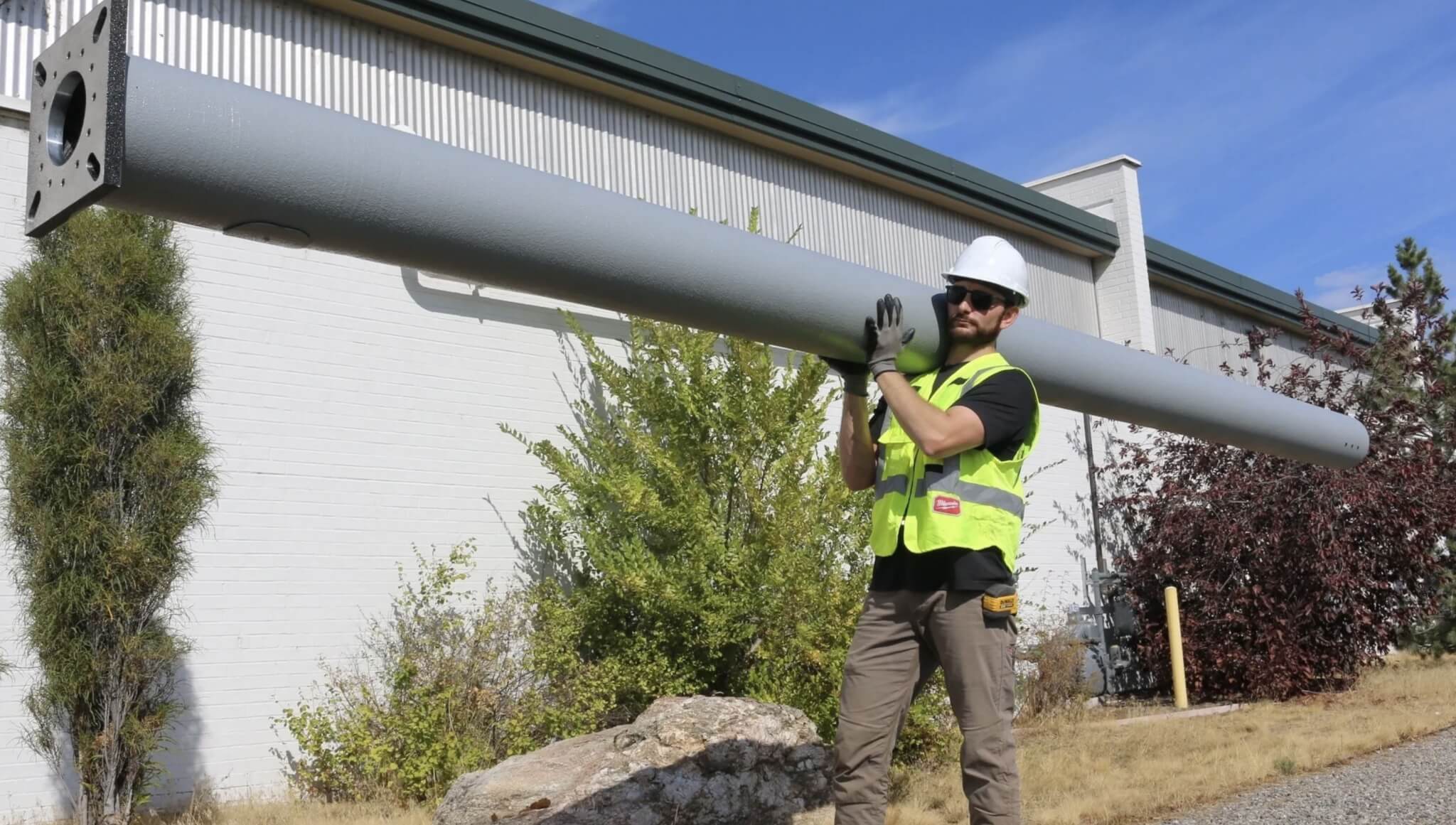