Navigating wind turbine blade standards
From 4,000-year-old windmills in Persia to floating wind turbines in the North Sea, wind energy has evolved from rudimentary technology to a highly advanced and strategic component of modern energy infrastructure. Today, the unique requirements of turbine design and lengthy qualification processes are molding its development. Here, Patricia Vázquez our carbon key account manager for wind energy explores how these factors influence the implementation of new wind blade designs, and the standards that guide their manufacture.
The diversity in design specification, components, materials and operational environments and condition can complicate production. OEM´s might specify blades with different lengths, profiles, or raw material weight fractions, to adapt to their own specific requirements. These range from thin, narrow profiles with several kilometers of material to thicker, larger plates for added rigidity.
Offshore blades, for example, are often more than 100 meters and must withstand immense loads. This added rigidity helps prevent excessive bending during operation, which could result in the blade striking the turbine tower.
All designs must meet consistent performance standards, including aerodynamic efficiency, strength, and fatigue resistance, provided in general standard like IEC 61400-5:2020 and DNV-ST-0376.Nevertheless, each design requires customized materials, production processes and extensive testing, leading to higher costs and longer production timelines.
To address these challenges, APQP4Wind was established to standardize quality assurance practices across the wind energy sector. This non-profit organization employs principles from Advanced Product Quality Planning (APQP) to streamline product development and approval processes. APQP4Wind aims to propagate consistency, reduce the cost of non-quality and accelerate time to market by standardizing documentation, testing, and quality assurance.
Testing and qualification
Qualification and testing of wind turbine blades are crucial to ensure they meet industry standards. Prominent and certified testing facilities in Germany and China are integral to this process, performing extensive evaluations of turbine component materials and designs. For instance, testing of the carbon spar cap supplied by Exel involves mechanical and fatigue examinations conducted by these external laboratories to validate compliance with the OEMs’ specifications.
These rigorous assessments validate that materials can withstand operational stresses and environmental conditions. Materials are tested for their durability and performance under simulated operational conditions. These include exposure to freezing, thawing, and high humidity to evaluate their resistance to environmental degradation.
After this, a pre-production approval process (PPAP) typically lasts three to six months, involving quality and paperwork checks on three to thirty blades. Delays can occur if customers need to adapt their manufacturing processes for new materials. Certification from bodies like DNV requires additional blade testing, also adding time and costs. This means that transitioning from initial requirements to serial production can take up to three years.
Navigating these challenges demands experience and innovation from the blade component manufacturers. As a pultrusion leader, we work closely with turbine OEMs to ensure compliance with standards. This includes customized manufacturing processes and qualification tests, ensuring each blade meets performance and safety criteria.
From ancient windmills to today’s advanced turbines, the wind power industry has made strides. However, as the sector continues to evolve, embracing standardization is key to giving blade manufacturers confidence in supplied components’ reliability, safety, and efficacy.
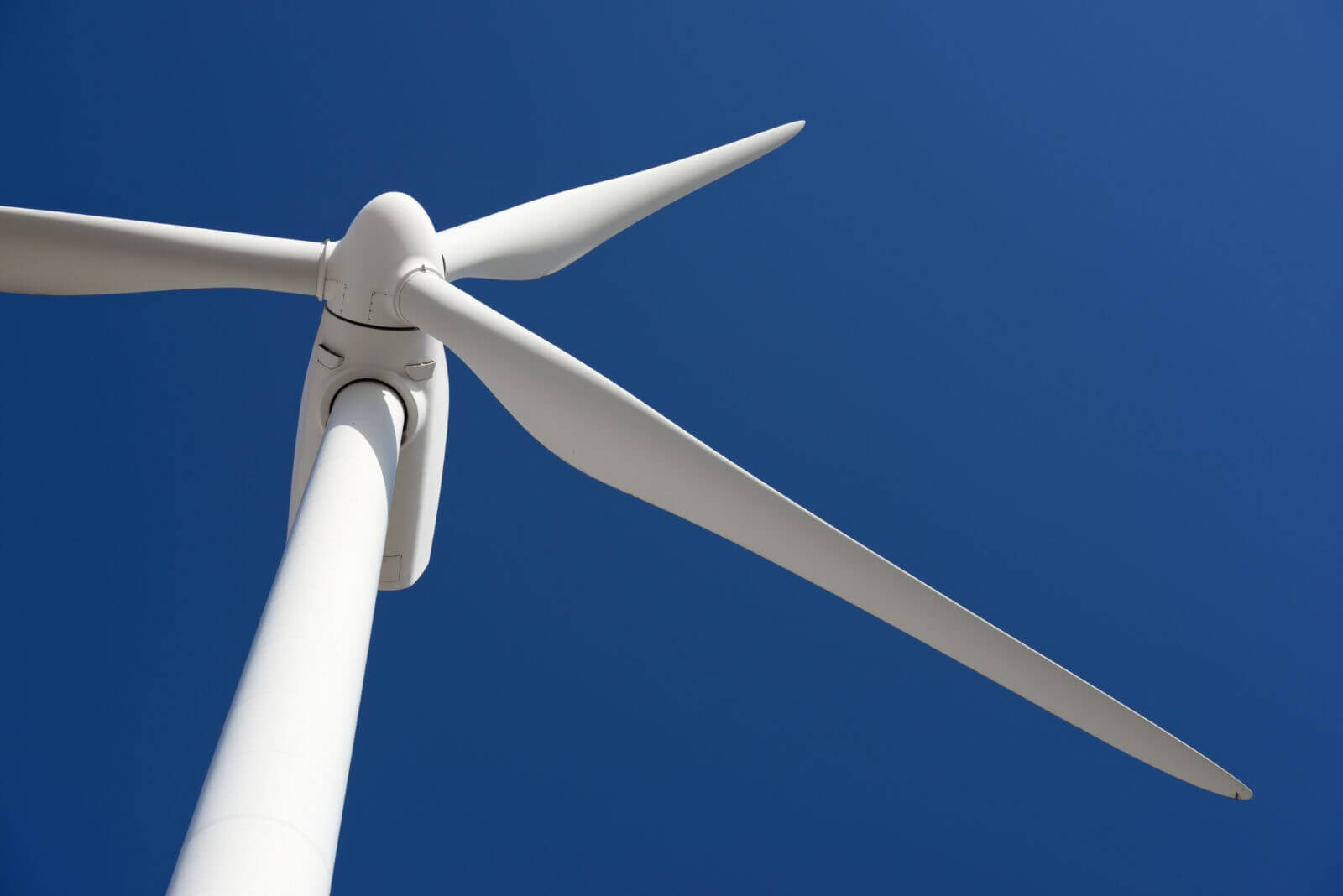